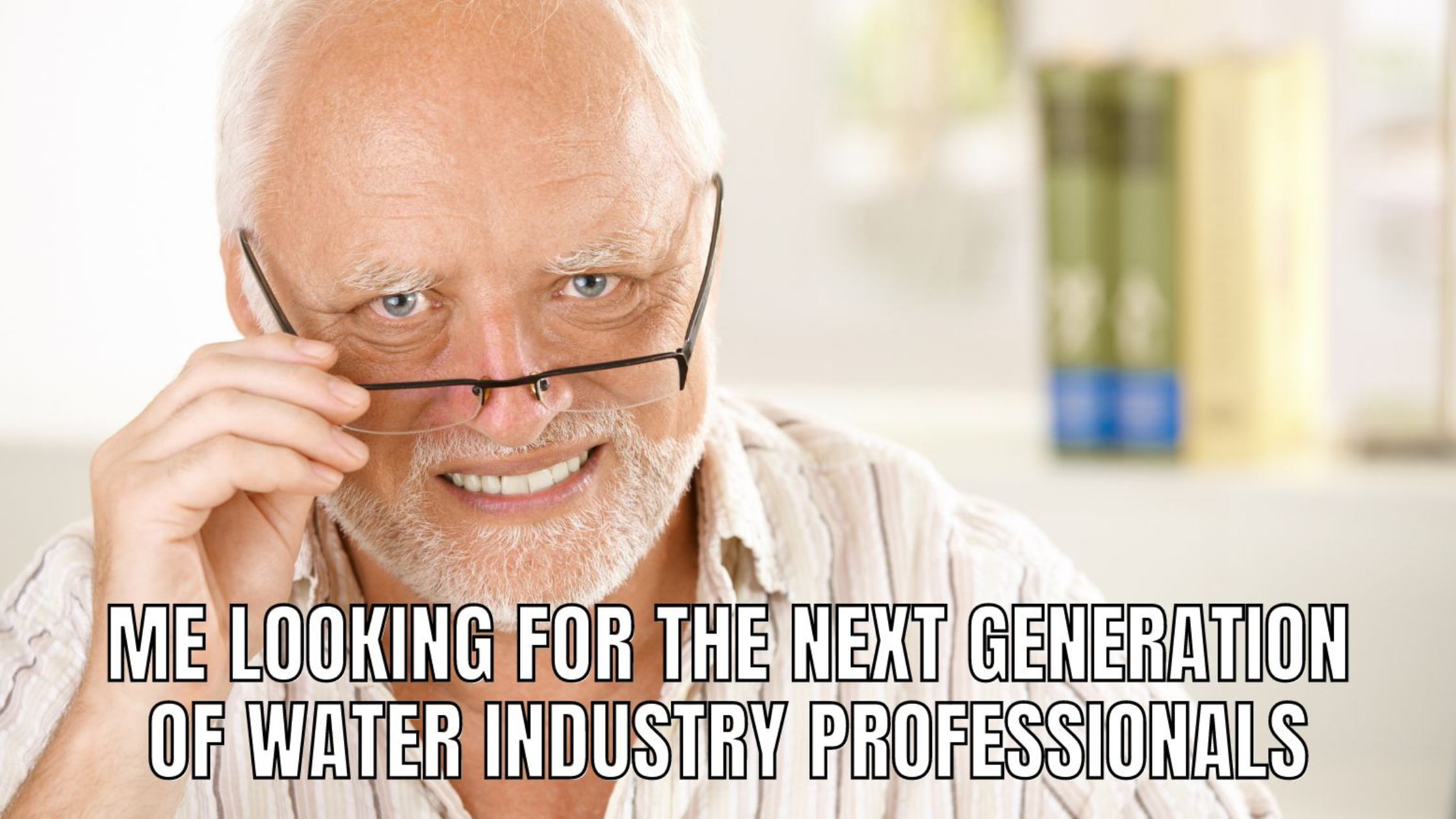
1 min read
America’s Water Industry at Risk Due to Retiring Professionals
The silver tsunami is upon us. A huge wave of baby boomers are now hitting retirement age and leaving the workforce. This mass exodus of experienced professionals presents a big challenge for utilities, who now have to find ways to transfer all that...
Read More