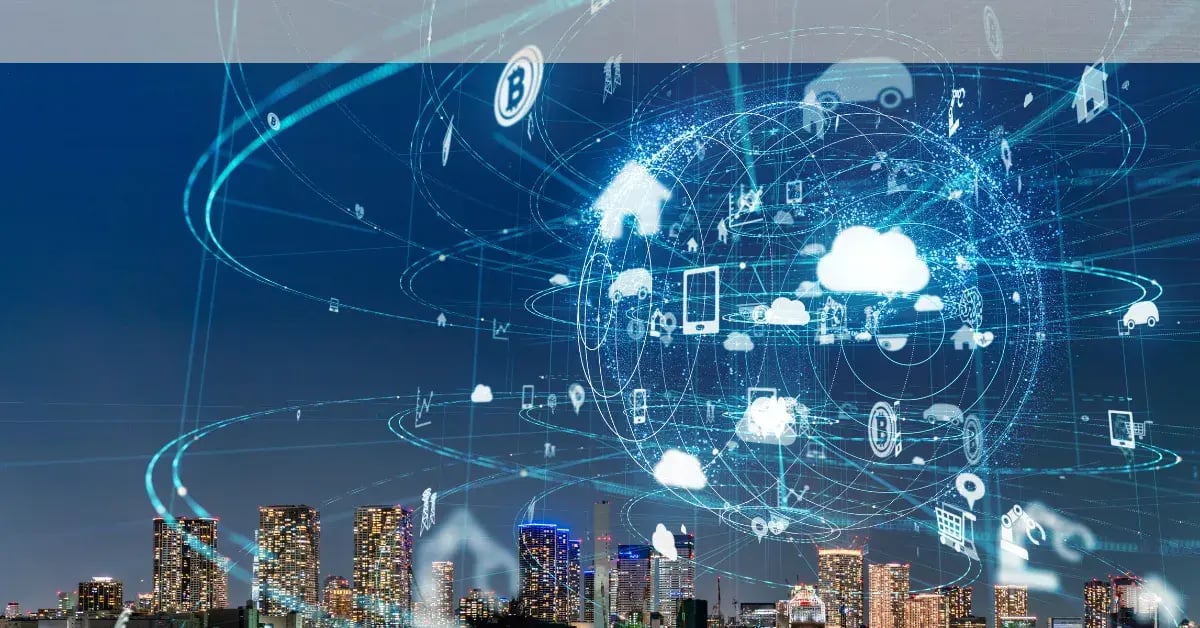
3 min read
Building Smarter Infrastructure with AI for Climate Change Adaptation
A major solution to fix aging infrastructure to adapt to climate change realities is building smarter – not bigger. When it comes to choosing the right technology to implement, we should look for smart INFRASTRUCTURE solutions that offer monitoring,...
Read More